American companies adopted the lean manufacturing system for some of its most alluring labor productivity improvements, especially the elimination of waste. But eliminating waste is only one component of the multi-faceted system, which starts with safety and quality. A company cannot reap the benefits of lean by implementing only a few of its components or tools.
A successful lean system requires meticulous attention to three interconnected subsystems: the operating system (value stream, flow, pull etc.), the management system (visual management or the incentives to drive safety and quality rather than overhead absorption) and lastly, the cultural system (continuous learning, problem solving, removing obstacles and dialogue).
This third system features the human feedback loop that becomes the behavioral engine for the other two. Companies will only reap the full benefit of lean if they succeed in bringing all three systems to life. While many manufacturing companies have made great progress around the operating and management systems, many rely on the cultural system to take care of itself. But lean’s success depends on the care and feeding of the cultural system; ignoring this element imperils lean’s overall impact.
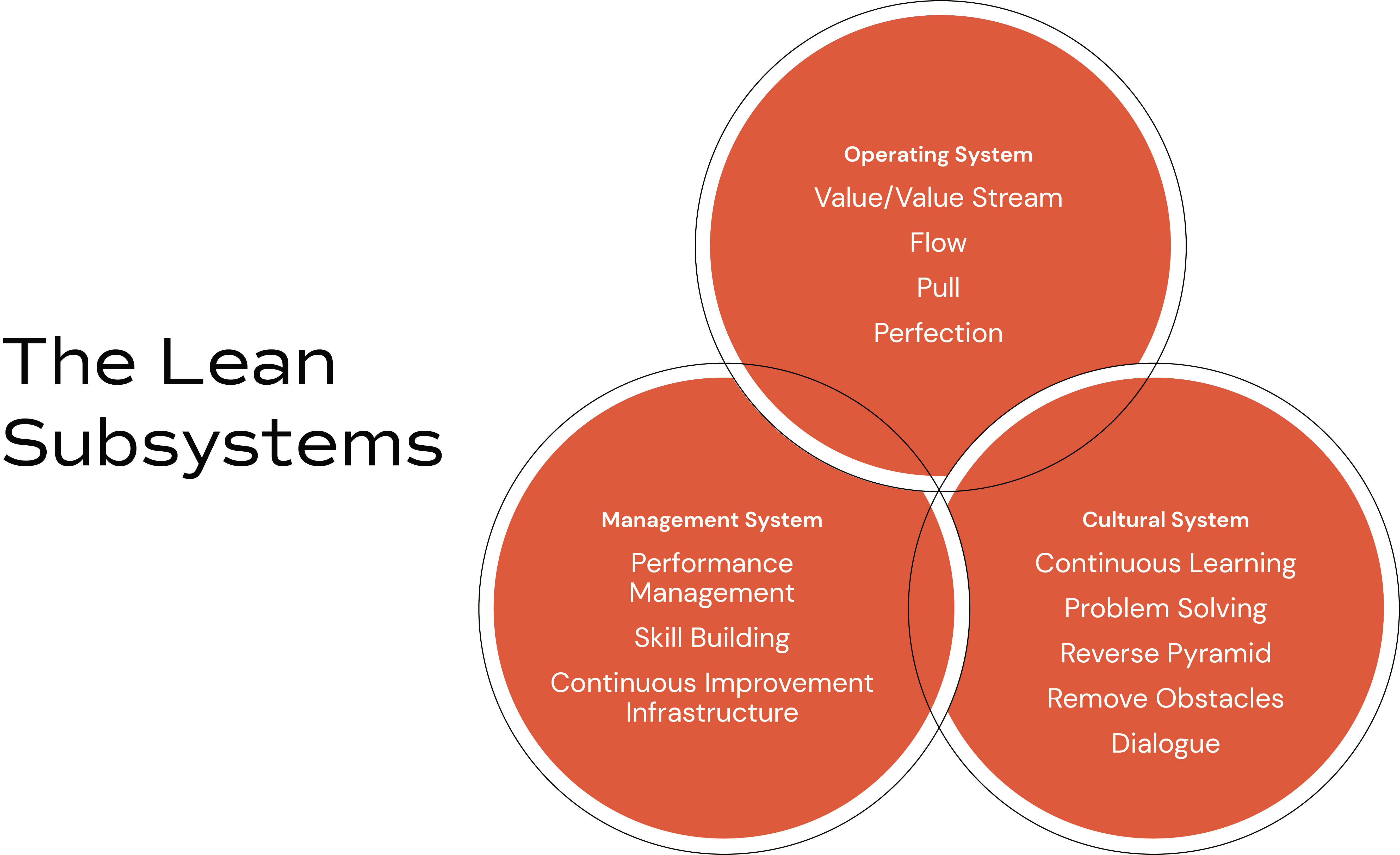
Nurturing Lean Culture
It’s not easy. Lean culture is arguably the most difficult component of the system, simply because altering the behaviors of people proves more challenging than introducing new concepts. Companies must recognize that a healthy cultural system, while nice-to-have in traditional manufacturing environments, is non-negotiable in a lean manufacturing operation. The fragile nature of lean means that even minor issues, left unaddressed, risk damaging the overall manufacturing system.
But a healthy culture system does not occur by management decree. Beautiful posters and pamphlets convince no one. Culture change can only occur when the entire organization viscerally understands (and appreciates) that front-line colleagues often hold the most critical information.
Unlocking this information lies at the core of lean success. Employees at every level – but especially at the front line – must feel empowered to communicate potential truths that others may not want to hear. They must listen in an engaged, curious manner, and most of all, trust one another. And they must be prepared to share difficult realities with colleagues several levels more senior, without discomfort or fear of retribution.
It’s about trust, respect and psychological safety
Respect and trust unlock these realities and honors their knowledge. Team huddles around established performance metrics are necessary but insufficient to achieve the open, continuous two-way communication mandated by the lean cultural system. In short, successful lean depends on psychological safety.
Psychological safety resides in the belief that no one will be punished for speaking up with ideas, questions, concerns, or mistakes. In a psychologically safe atmosphere, people feel comfortable to question assumptions and respectfully disagree. Such an environment requires people of all levels to embrace three core competencies:
1. To ask questions: not leading questions or verbal traps, but rather open and humble inquiries about a specific problem
2. To listen: not with the intention to reload your next question that shows how smart you are, but to listen actively, with an open mind and open heart
3. To connect: the different perspectives of people and the different facts that allow the collaborative development of the best answer.
The steady drum beat of delivery pressure and operating targets often distract companies from attending to these important skills. And many companies don't know how to build this culture of psychological safety that holds up in moments of crisis.
Practice matters
This is where Reflection Point (formerly Books@Work) comes in. Reflection Point builds psychological safety by creating the conditions to practice these skills. We provide a platform for participants to speak openly about what they believe. The open dialogue invites all voices, pulls participants out of silence, and creates an environment that’s both secure and stimulating. Most importantly, participating companies see significant improvements in the core indicators of psychological safety, like willingness to take risks, and comfort in speaking up even when others may disagree.
Marvin Riley, Executive Vice President and COO of EnPro Industries, has seen this result play out at every level in his company:
"Reflection Point provides an experiential learning environment that facilitates connection, relatedness and full authenticity. It is much easier to express a different point of view or to suggest something radically new if you have already practiced during a Reflection Point session."
And, Riley adds, this comfort translates directly to work:
"The person closest to the problem or a situation must feel empowered to speak up in order to get past a problem's symptoms to its root cause. My experience with Reflection Point has been profound; everyone with whom I've done a Reflection Point session feels much more comfortable to tell me what I need to hear instead of what they think I want to hear."
The lean system is intentionally fragile so that processes are made robust and fault free. But lean will never be fault free without a willingness to embrace all three subsystems: operations, management and culture. Only with the latter will a company build the psychological safety necessary to properly execute a lean system.
If you believe your company should be able to improve faster given all the investments you have made in lean, ask yourself whether your culture is where it needs to be. You might be surprised by how a small investment in culture will go a long way.